Work management processes don't mean having more to do. They mean getting more done.
Most large organisations have enough to think about. Processes, initiatives, projects, visions, structure, staffing, objectives... the list goes on. And it’s constantly evolving.
So when we come along and suggest changes to the work management process, it can be greeted with a certain amount of resistance. Who needs yet another change when they’re already dealing with a maelstrom of change every day?
In reality, work management isn’t one more thing to do. In fact, it’s the way to get things done. Get that right, make it as efficient and effective as it can be, and it becomes the vehicle that not only delivers the work that needs done, but also articulates the need for that work in the first place.
Let’s take some examples of how that might work:
BUILDING GOOD BUDGETS
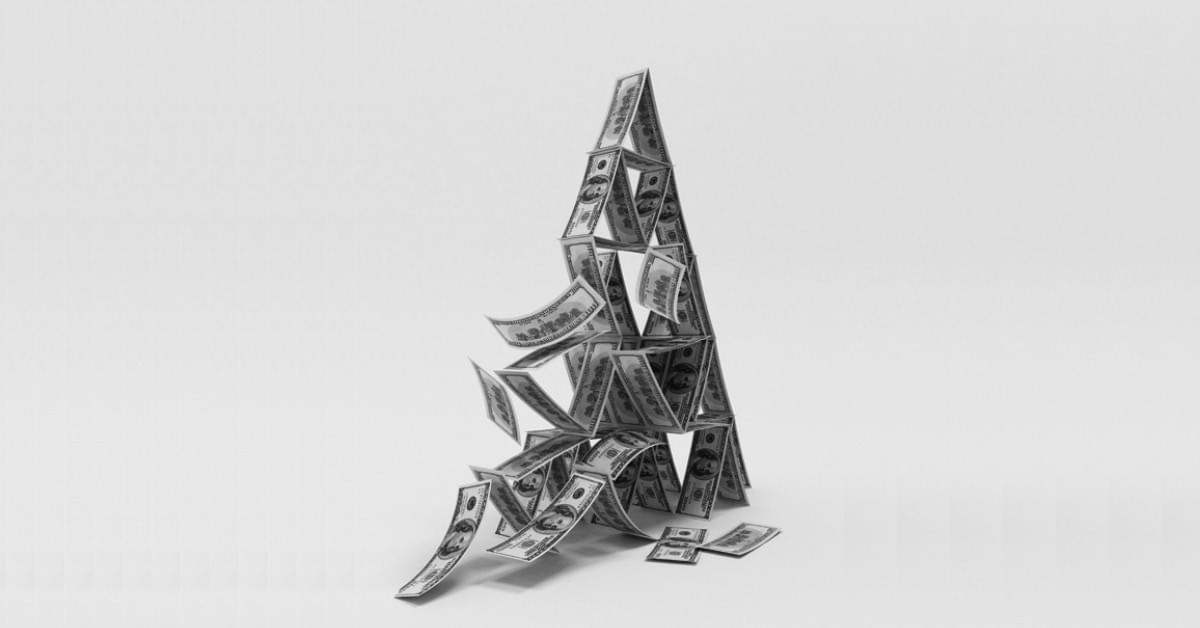
If an organisation needs to reduce its maintenance budget, it might implement that reduction by changing the work management process to re-prioritise new and existing work. Ongoing work that falls below the prioritisation threshold gets shelved, and anything new is stopped as it comes in.
Alternatively, the process could focus on the point of approval, with greater emphasis placed on reviewing the whole cost of completing the work. That means looking beyond hours and work method to cost of tools, equipment, supplies, time off other jobs etc. If the impact on budget is over a set standard, the work is suspended or refused.
SETTING THE STRUCTURE
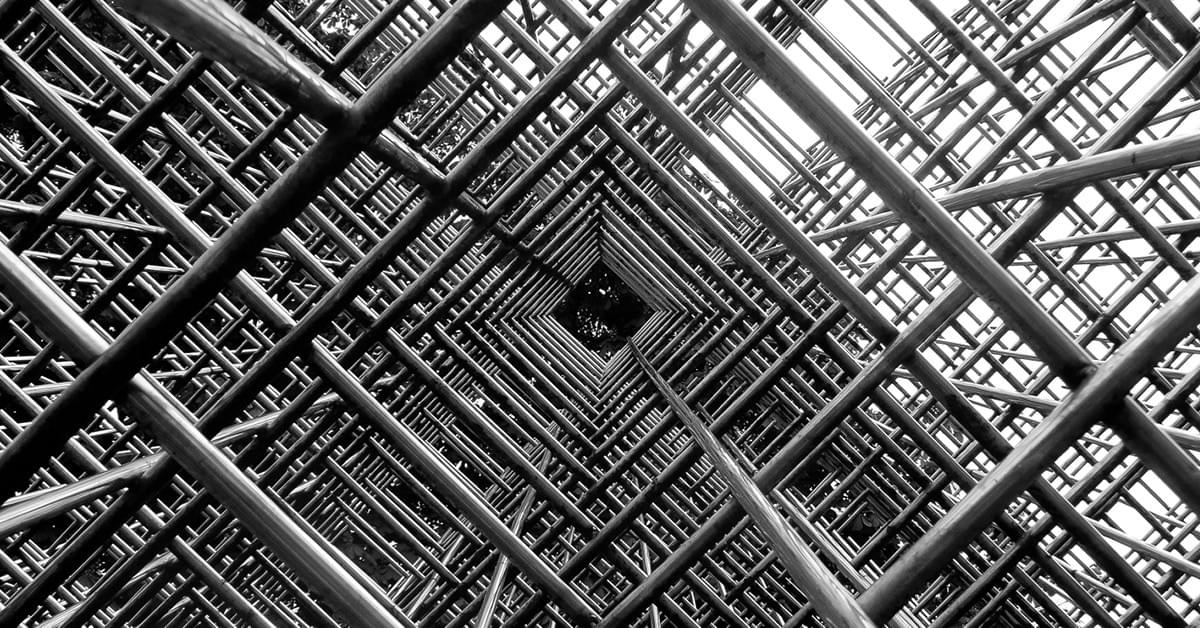
Say an organisation makes changes to its structure. The work management process can help embed that structure. If, for example, there’s a new onshore support team responsible for executing high complexity activity, the work management system automatically identifies high complexity activity and assigns it to the correct team.
It will also monitor their effectiveness, helping to ensure that structural changes are not only embedded, but monitored, evaluated and amended if necessary.
LOOKING AT LOSSES
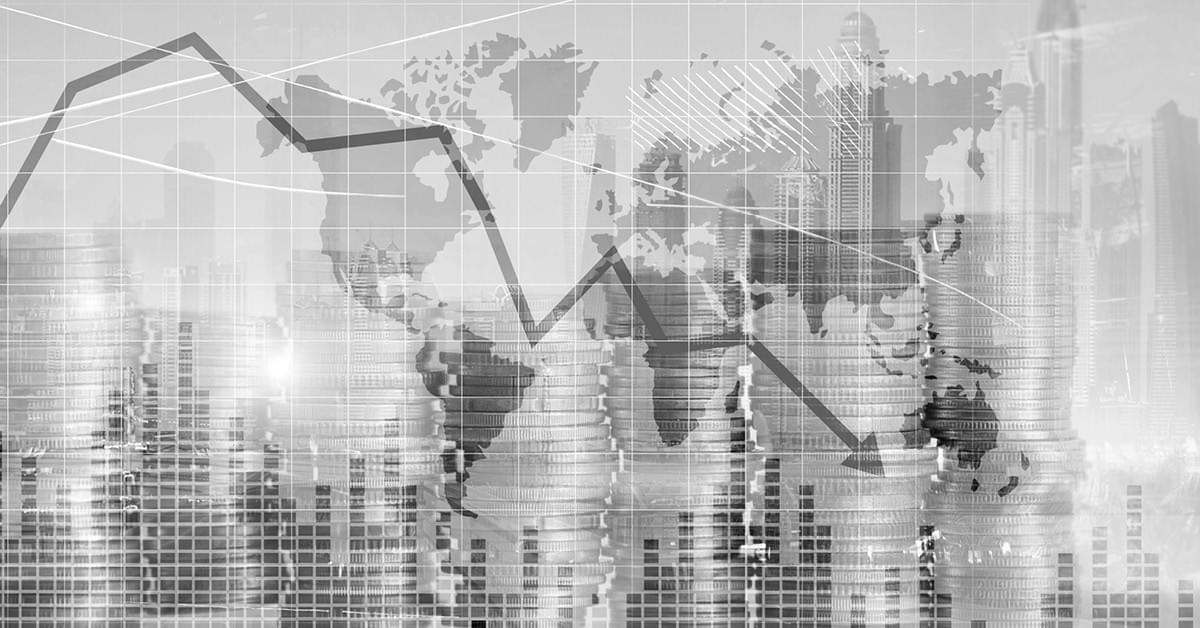
Whether we’re looking at large or small losses, the work management process has a role to play. It can direct a team (or teams) to focus on corrective maintenance activities according to their production consequences — low, high or both. Identifying the issues allows for a tailored and effective response.
It’s tempting to look at changing or implementing a work management system as just one more thing to be done, one more problem to solve. But when the system is used correctly, it becomes the vehicle for implementing and articulating necessary change everywhere else.
Which means you get more done — and get it done right.
#SRCN/Articles